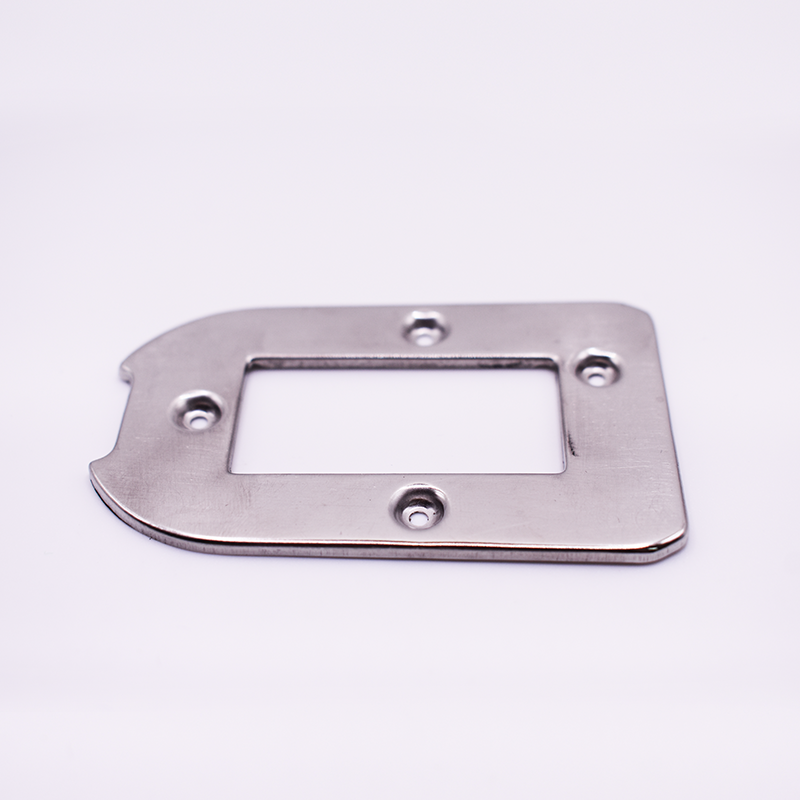
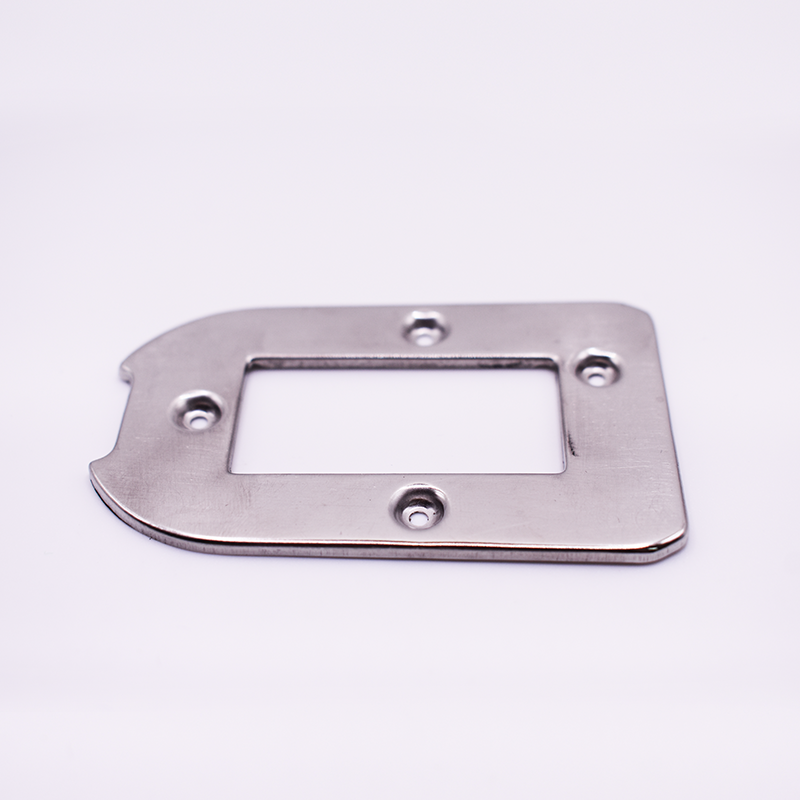
- Product Detail
-
Material Selection and Preparation
Material Selection: Steel sheets, aluminum sheets, and copper sheets are generally used in sheet metal processing. Depending on the application and performance requirements, for example, appropriate steel sheet is selected for automotive parts in consideration of strength and corrosion resistance, while aluminum sheet is selected for electronic device housings where light weight and conductivity are required.
Material inspection: For the selected material, we inspect its thickness, flatness, material composition, etc. to confirm that it conforms to the standard.
Pre-cutting treatment: If necessary, we remove oil, rust, and other contaminants from the surface of the material to prepare it for cutting and bending.Cutting Process
Die cutting: Metal sheets are punched into a predetermined shape using a die. Die cutting is efficient for mass production and produces high-precision shapes with good reproducibility.
Laser cutting: Metal sheets are cut by melting and vaporizing them using a laser beam. It can accommodate complex shapes and materials of different thicknesses, and is characterized by its smooth cutting surface and high accuracy.
Milling cut: Using a milling machine, a metal plate is cut by a rotating blade. It is suitable for cutting relatively thick plates and special shapes, and offers a high degree of processing flexibility.Bending
Bending with a break press: A break press is used to bend metal sheets using a die. The bending angle and radius can be accurately controlled, enabling stable bending.
Roll Forming: Using a roll former, a metal sheet is pressed and bent with a roll to form a cylindrical or curved surface. This process is suitable for bending large-area sheets or creating shapes with a certain curvature.Welding Processes
Arc welding: Arc discharge is generated between the electrode and the object to be welded, melting the welding rod or wire and welding it to the joint to join parts. Strong joints are possible, and the process can be applied to a wide variety of metal materials.
Laser welding: Laser light is focused to achieve a high energy density and melts the metal to be joined. Welding speed is fast, heat-affected zone is small, and high-precision welding is possible. It is particularly suitable for joining thin sheets.Surface Treatment
Coating: Coatings are applied to the surface of metal sheets to prevent rust and improve their aesthetics. Spray coating, electrostatic coating, and other methods are available, and the color tone and luster can be freely selected.
Plating: Electroplating, hot dip plating, and other methods are used to form zinc, chrome, nickel, and other metal coatings on metal sheet surfaces. Corrosion resistance can be greatly improved.Assembly and Inspection
Assembly: After processing and surface treatment, each sheet metal part is assembled as designed. Parts are fastened together using screwing, clip fastening, welding, or other methods to assemble the finished product.
Inspection: Final inspection is conducted on dimensional accuracy, appearance, function, etc. Dimensional accuracy is checked using measuring instruments, external appearance is checked for scratches, pinholes, uneven paint, etc., and functional aspects are checked for operation and strength tests to ensure product quality.
Sheet metal processing
Material: SUS Processing method:Sheet metal processing Processing time: 5-7 days
Category:
Keywords:
Sheet metal
Factory Display
Q&A
Related Products